在鋁合金壓鑄生產中,拉傷問題頻發,不僅降低鑄件合格率,還增加生產成本。要解決這一問題,需先明確其產生原因,再對癥下藥。
拉傷的首要原因是模具表面質量不佳。模具表面若存在粗糙、劃痕或脫模斜度不足,鋁合金液在凝固收縮時,就易與模具表面產生較大摩擦力,從而導致拉傷。其次,脫模劑使用不當也會引發問題。脫模劑噴涂量不足、分布不均或質量不達標,無法在鑄件與模具間形成有效隔離層,拉傷風險大增。此外,壓鑄工藝參數設置不合理,如壓射速度過快、保壓時間過長,會使鋁合金液對模具表面的沖擊力和壓力過大,同樣會造成拉傷。
針對模具表面質量問題,可通過精細加工和拋光處理來改善。采用高精度加工設備,確保模具表面粗糙度達標,并對易產生拉傷部位進行鏡面拋光,減少表面摩擦系數。同時,合理設計脫模斜度,一般鋁合金壓鑄脫模斜度在 1° - 3° 為宜,復雜結構需適當加大。
在脫模劑使用方面,要選擇質量可靠、適配鋁合金壓鑄的脫模劑。嚴格按照工藝要求控制噴涂量和噴涂方式,確保脫模劑均勻覆蓋模具表面,形成完整隔離膜。可采用自動化噴涂設備,提高噴涂精度和效率。
優化壓鑄工藝參數是關鍵。根據鋁合金材料特性和鑄件結構,合理調整壓射速度和保壓時間。降低壓射速度,可減少鋁合金液對模具的沖擊力;縮短保壓時間,能避免鑄件過度受壓。通過多次試模,找到zui佳工藝參數組合。
此外,定期對模具進行維護保養也很重要。及時清理模具表面殘留的鋁合金碎屑和脫模劑積垢,檢查模具表面磨損情況,對磨損部位進行修復或更換,保持模具良好工作狀態。
通過以上多方面措施的綜合應用,可有效解決鋁合金壓鑄的拉傷問題,提高鑄件質量和生產效率,降低生產成本。
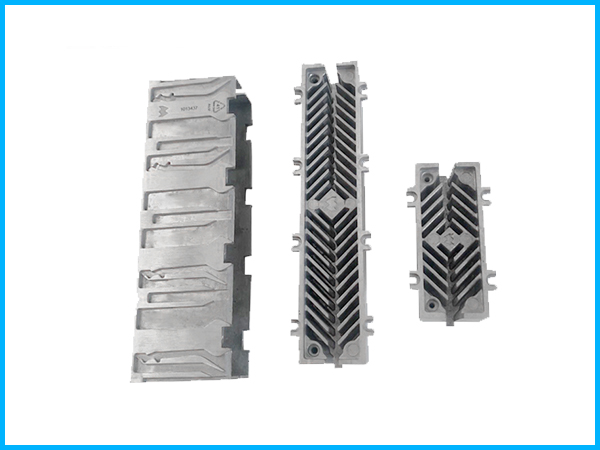